13 Common BNC Connector Installation Mistakes
Every installer has his or her own tips and tricks for installing a BNC connector on coax cable. But when bad habits lead to having to re-terminate connectors, labor time and scrap costs increase - and so does frustration.
Even in cases where the connection technically works, it may still negatively affect system performance. Read on to discover the 13 most common BNC connector installation pitfalls and how avoid them - improving reliability as a result.
Connector Selection Mistakes
1. Selecting the wrong connector size
Never force a plenum connector onto a non-plenum cable or an RG-6 connector onto an RG-59 cable. Use Belden’s cable-to-connector cross-reference guide to make sure you have the right BNC connector size, or check the manufacturer’s recommendations and dimensions.
2. Choosing the incorrect bandwidth
If you are installing 4.5 GHz coax, make sure the BNC connectors you select are also guaranteed to that same level of performance. Other BNC connectors may only work to 1.5 GHz or 3 GHz. If you are installing a 4K coax cable, double check to make sure the BNC connector you select is also rated appropriately (If it's a Belden 4K coax cable, the connector should be rated to 6 GHz or 12 GHz.)
3. Judging a connector by looks alone
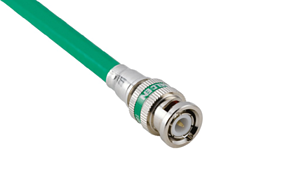
Choosing a BNC connector with the correct impedance is an important step in maintaining system performance; however, if you follow the belief that 50 Ohm connectors look a certain way, and 75 Ohm connectors look a certain way, you may be mistaken. Can you tell what type of connector is shown?
This is a 75 Ohm connector - but does it look like one? Don't judge a connector only by its looks. Refer to the technical data sheet to choose the right impedance.
4. Ignoring compression connectors
Crimp connectors leave the coax crimped in a hexagon shape. Physical changes like these affect the electrical performance of the cable. Compression connectors use a 360-degree compression to maintain concentricity of the coax. For the best performance, locking BNC connectors limit movement in the connector body and deliver return loss performance that exceeds -20 dB at 4.5 GHz.
Stripping and Preparing Mistakes
5. Using electrical dykes to cut coax
Electrical dykes are not designed to cut coax. They will flatten the cable’s dielectric, which changes the cable’s physical structure and results in performance issues. We recommend cutting coax with cable cutters that have curved jaws that don’t flatten the dielectric.
6. Using the wrong strip tool
Belden compression connectors require a ¼" x ¼" strip, which results in a ¼" center conductor and ¼" dielectric and braid. If you're using the wrong strip dimensions, the cable won't fit in the connector the way it was designed. For three-piece crimp connectors, always prep the cable according to the installation instructions.
7. Using a dull prep tool.
Dull tools can cause the braid to wrap around the center conductor, causing a short; long braids hanging out the back of the connector can create a moisture path.
8. Over-twisting with a strip tool or using a razor/knife to strip the cable
Three rotations forward and three rotations back is the proper way to use a strip tool. Installers who use more rotations, or use a razor to strip the coax, run the risk of nicking the center conductor and impacting performance.
9. Forgetting to flatten the foil
Flattening the foil prevents bunching. When foil bunches up inside the cable, the center pin won't fully extend and lock in the front of the cable.
10. Letting one strand of the braid go inside the connector
Failure to keep all the strands from touching the center conductor will cause a short. Use a tool with a braid flare feature, or put a strip of Velcro on the side of your strip tool to help "brush" the braid away from the conductor.
11. Pulling hard to “test” the connection
Before you pull on the BNC connector, keep in mind that there is a maximum pull tension on the cable. If you pull too hard to test the connector, you may exceed the pulling tension of the cable, resulting in poor performance.
Crimping and Compressing Mistakes
12. Using the wrong crimp die.
When the wrong crimp die is used, the crimp isn’t shaped correctly and can negatively impact performance.
13. Failing to push the center conductor/pin to the proper location.
With some compression connectors, it is not possible to over-insert or push the cable too far into the connector; however, when not pushed in far enough, the connector’s center pin will not be fully extended to the edge of the connector.
To see proper BNC connector installation techniques in action, watch:
Installing Pro-SNS Connectors
Installing Brilliance HD-BNC Connectors